Air Cooling Pelletizer (Die-face Cutting)
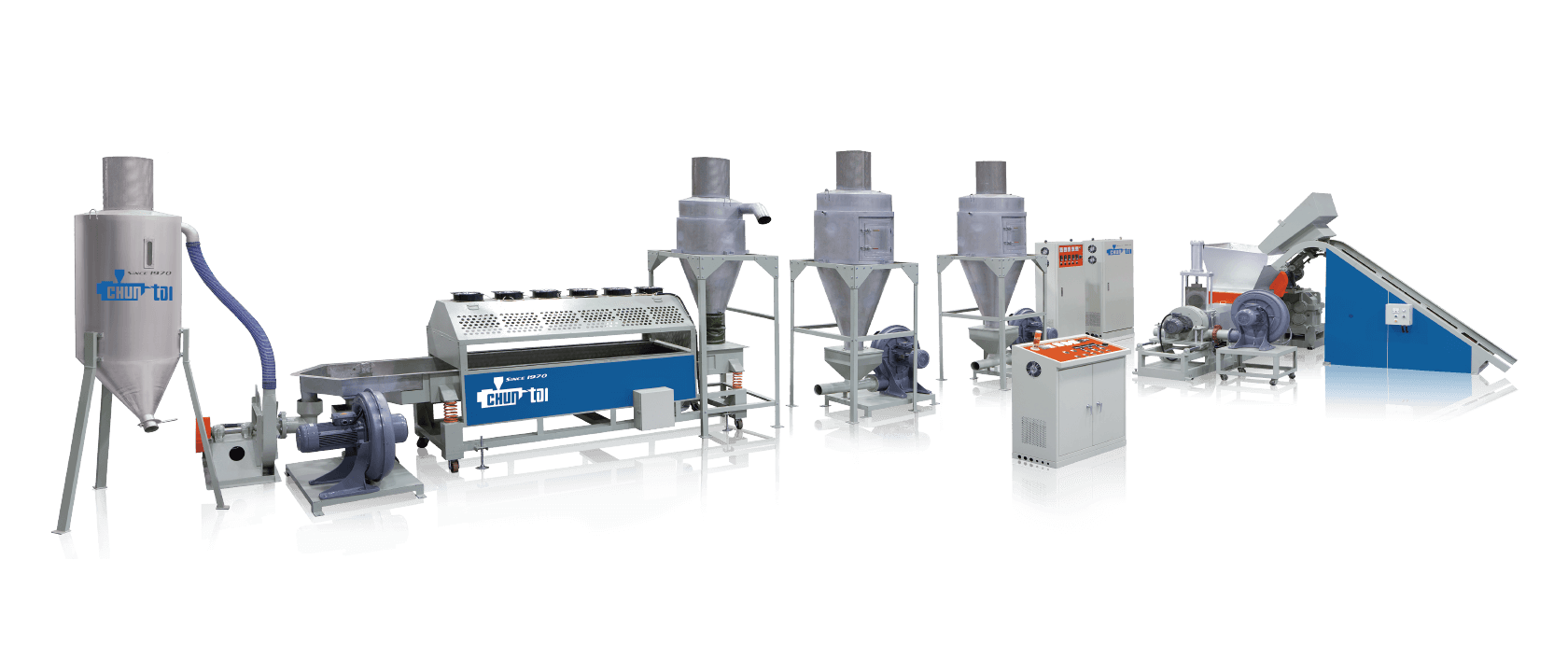
Product Overview
The Air Cooling Pelletizer (Die-Face Cutting) is engineered for thermally sensitive materials such as TPR, EVA, and PVC, where traditional water cooling methods may cause deformation or surface defects. This system utilizes a rotary die-face cutting mechanism combined with a dual cyclone air cooling chamber, enabling simultaneous cutting and rapid air drying. The result is clean, uniform pellets with excellent surface quality and no water-related marks. Designed for seamless integration with kneaders or compounders, the machine supports automatic feeding and precise temperature control. It is ideal for applications involving footwear-grade materials, elastomer pellets, and specialty compounds that require non-water cooling environments.
Key Features
- Air-Cooled Die-Face Pelletizing: Purpose-built for materials sensitive to water or heat degradation, ensuring surface integrity and processing reliability.
- Rotary Cutter Head: Features adjustable cutting angles and a quick-change blade system to simplify maintenance and improve flexibility.
- Dual Cyclone Air Cooling System: Delivers consistent, uniform cooling to maintain pellet shape and surface quality.
- Compatible with Multiple Formulations: Supports various elastomers and PVC compounds, including TPR and EVA-based materials.
- Upstream Integration Ready: Can be directly connected to kneaders or compounders with support for automatic feeding systems.
- Manual Pellet Size Adjustment: Cutting speed and pellet size can be adjusted manually to meet different product specifications.
- Flexible Output Options: Finished pellets can be packed directly or transferred through an optional screener and storage system.
- Fully Integrated Workflow: Covers feeding, extrusion, cutting, and air cooling in a streamlined four-stage process.
Applications
- Elastomer-Based Products: Such as TPR shoe materials, EVA granules, composite TPR layers, and PVC pellets.
- High-Fill & Heat-Sensitive Compounds: Formulations that are incompatible with water cooling, including high CaCO₃ content or sensitive elastomers.
- Functional Granules for Secondary Processing: Including materials for wire coating, soft elastic sheets, and other pre-compounded granule-based applications.
Technical Specifications
Item | Specification |
Applicable Materials | TPR, EVA, PVC |
Pelletizing Method | Die-face cutting with integrated air cooling |
Cooling System | Dual cyclone air chamber with external blower and adjustable airflow |
Cutter Design | Rotary cutter with adjustable angle and quick-change blades |
Temperature Control | Precision control in pelletizing zone |
Pellet Size Control | Manual adjustment of cut speed and pellet size; no automatic sizing |
Workflow Coverage | Integrated process: feeding, extrusion, cutting, air cooling |
Downstream Handling | Supports direct packaging or transfer via optional screener/storage tank |
System Integration | Compatible with kneaders or compounders; supports automatic feeding |
FAQ
Q1: What types of materials is this system suitable for?
A1: The system is designed for TPR, EVA, and PVC. It does not support TPU or high-fill compounds such as those with excessive CaCO₃ content.
Q2: Why use air cooling instead of water cooling?
A2: Air cooling prevents thermal shock, surface defects, or material degradation that may occur with water cooling, especially for heat-sensitive or specialty compounds.
Q3: Is the cutter head adjustable and easy to replace?
A3: Yes. The rotary cutter design allows for quick angle adjustments and easy blade replacement for efficient maintenance.
Q4: Does the system include a dual cyclone air cooling chamber?
A4: Yes. The dual cyclone system is standard and ensures uniform, high-efficiency cooling to maintain pellet shape and consistency.
Q5: Can the pellets be packaged directly after cooling?
A5: Yes. Pellets can be packed directly or optionally routed through a screener and storage bin depending on your workflow needs.
Q6: Does it support automatic feeding or upstream connection?
A6: Yes. The system supports automatic feeding and can be integrated with kneaders or compounders. However, automatic discharge and screening modules are optional.
Q7: Is the pellet size consistent? Does it offer automatic control?
A7: Pellet size and cut speed can be adjusted manually. Automatic sizing is not included in this model.